FiberBed Air Filter Vs. ESP's System
Air Clear Fiberbed Filters Systems have proven over the past 30 years to be superior to Electrostatic Precipitators (ESP's) for the control of Textile Dryer Emissions. Benefits of the Air Clear Fiberbed Filter System include:
- Significantly higher run time with reduced maintenance that results in increased profitability for your facility.
- Less cost than ESP maintenance
- Lower operating cost
- High removal efficiency performance
There are three areas that set the FiberBed Filter technology apart from ESP's:
Performance:
A properly designed ESP and a FiberBed Filter System will both provide 0% opacity initially. However, as the contact surfaces on an ESP collect the particulate material the efficiency gradually diminishes until the ESP requires cleaning.
Where the start point efficiency is at or near 99%+. Almost immediately, by the various nature of the ESP’s design, the surface get dirty and the efficiency begins to fall off eventually reaching a point where the visible emissions are above the limit. This requires cleaning of the ESP system so that the surfaces are able to remove a higher level of particles and return near to its original performance. The cleaning process is never able to clean the ESP surfaces to their original state, so after several cleanings the ESP requires a major overhaul to meet visible emission requirements.
FiberBed Filters maintain a constant removal efficiency throughout the filter life. As the filters get ‘saturated ‘ with particulate, the only thing that changes is that the pressure drop increases requiring more energy to move the process exhaust through the filters. The opacity control remains at or near Zero throughout the filter life of 2-4 years depending on the process.
The new China regulations (DB/33-962) for opacity are so stringent that thousands of ESP’s are now or over the next two years will be replaced with FiberBed Filters.
Case Study
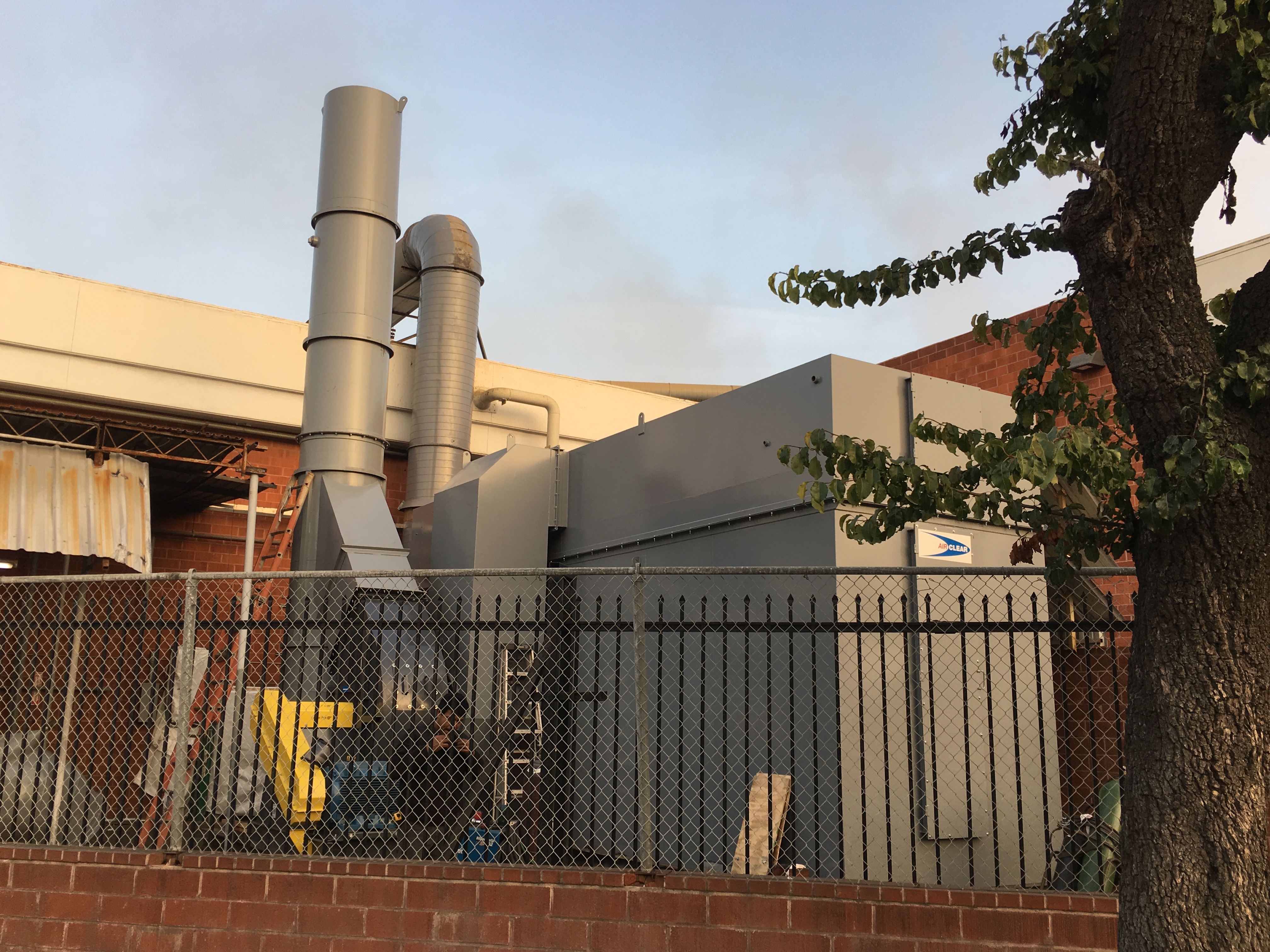
Fiberbed Mist Collector System. Pacific Continental Textile, Compton, CA. 1 of 9 ESP’s replaced.
Maintenance:
As mentioned above, the Electrostatic Precipitator (ESP) needs frequent maintenance to remain in compliance. Depending on the products being produced, the production input and the type of ESP (Dry vs. Wet). A dry ESP adds a second layer of maintenance. The cooling section is normally an air-to-water or air-to-air heat exchanger. In either case, the emissions common to the textile industry coat the cooling surfaces reducing the cooling effectiveness and thereby increasing the inlet temperature which negatively impacts the performance of the ESP. One ESP may require a day of down/week just to clean the cooling system, and perhaps another day for the ESP itself. The wet ESP uses water/direct contact for cooling. The water eliminates the maintenance of the heat exchanger, however the water is directly in the electroplate zone. This, over time, can cause serious operational problems.
The The Air Clear FiberBed Filter Mist Collector only requires a major maintenance effort once every 2 to 4 years for replacing of the filters. This provides significant operating run time when compared to the required ESP maintenance. (two days maintenance to remove and replace the FiberBed filters). Weekly FiberBed Filter Mist Collector maintenance amounts to removal of collected oils every 1 to 4 weeks and the normal routine maintenance on fans and pumps, all of which can be done during operation. The Air Clear FiberBed Filter System is a fully automated PLC controlled system designed for optimum performance with the lowest amount of manpower attention. The result is increase operating time, a shift from maintenance personnel to production personnel due to increased availability for production.
Fire Risk:
Both the ESP and FiberBed air filters have a potential inherent fire risk. Due to the introduction of the high voltage, the potential for short circuits causing a fire is much greater in an ESP system. The FiberBed Mist Collector System has a first stage water scrubbing section, which makes transfer of fire from the process to the FiberBeds themselves nearly impossible. Fires in ESP’s occur with such frequency that insurance carriers have been cancelling or denying insurance coverage on processes using ESP’s. ESP’s damaged or destroyed in a fire are mandated to be replaced with an alternative technology. In addition to the cyclonic quench section, Air Clear FiberBed Filter units incorporate a complete fire suppression section integral to the unit, inlet and outlet fire detectors, flow switch interlocks to insure water supply and cooling, a fan ‘shutdown’ interlock, a pump ‘on’ interlock, and complete interface to the plant’s fire alarm system. Air Clear has replaced 9 ESP’s in the textile mills in the South Coast Air Quality Management District (LA) with our FiberBed Filter Mist Collector Systems. We have also replaced ESP’s in other locations in the USA, China and Korea.