How to Select Air Pollution Control
Products for Asphalt Roofing Manufacturing
The asphalt roofing manufacturing process yields products that are indispensable to modern society — namely, the shingles that cover the roofs of our homes and businesses and shelter them from the elements.
It does, however, result in the generation of hazardous air pollutants (HAPs) that dirty the air if left unmitigated. These HAPs are volatilized during asphalt processing because they are heated and agitated, and because of the oxidation reactions that occur in the blowing still. Sources of particulate matter and gaseous HAP emissions include asphalt storage and process tanks, asphalt blowing stills, asphalt loading racks, saturators, wet loopers, coating mixers, coaters and sealant and adhesive applicators.
To comply with emissions requirements, HAP filters must be used to remove them from the exhaust stream, an objective that can be accomplished by deploying air pollution control (APC) equipment. When selecting pollution control products, manufacturers must consider three questions. Does the APC equipment keep us in compliance with environmental regulations? Does the APC equipment require maintenance and downtime? What is the cost to keep the APC equipment in operation?
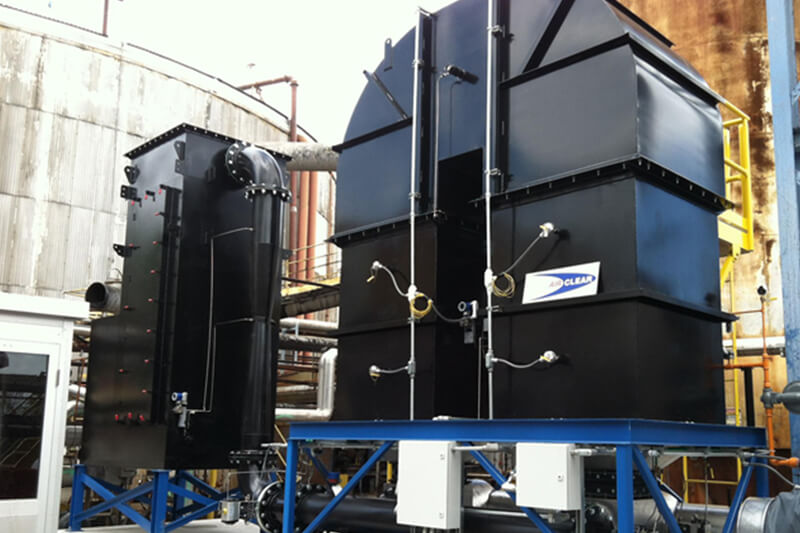
Figure 1: 2,500 SCFM Regenerative Thermal Oxidizer (RTO) preceded by a Coalescing Fiberbed Mist Collector System controlling emissions from an asphalt roofing and shingle manufacturing process. The mist collector protects the RTO’s ceramic media from fouling.
Environmental
Regulations
The Code of Federal Regulations Citation 40 CFR Part 63 Subparts LLLLL and AAAAAAA establish national emission standards for hazardous air pollutants (NESHAP) for major and area sources involved in asphalt processing and asphalt roofing manufacturing. These standards stipulate that asphalt processing facilities and asphalt roofing manufacturing lines must operate and maintain APC and monitoring equipment. Emissions are limited for two pollutants: total hydrocarbons and particulate matter.
Two APC systems from Air Clear™ LLC can help meet the requirements of emissions standards: Air Clear Coalescing Fiberbed Mist Collectors and Regenerative Thermal Oxidizers (RTO).
Air Clear Coalescing Fiberbed Mist Collectors capture, collect and remove the liquid mists, aerosols and submicron particles that cause opacity, smoke and blue haze. Coalescing fiberbed technology utilizes impaction, interception and Brownian diffusion to eliminate aerosol mists and submicron particles from virtually any gas stream. Air Clear Coalescing Fiberbed Mist Collectors are guaranteed to reduce stack opacity to five percent or less, excluding steam and uncondensed materials, and offer very high particulate removal efficiency, in excess of 99 percent.
Air Clear’s RTOs eliminate HAPs, volatile organic compounds (VOCs) and odorous emissions in exhaust gas by converting hydrocarbons to CO2 and water vapor in a high-temperature thermal oxidation combustion process. They eliminate as much as 99 percent of VOCs, exceeding the Environmental Protection Agency requirements for the following Clean Air Act requirements:
• Maximum Achievable Control Technology (MACT)
• Best Available Control Technology (BACT)
• Lowest Achievable Emission Rate (LAER)
• Reasonably Available Control Technology (RACT)
A combined APC system consisting of a Fiberbed Mist Collector and an RTO can be particularly effective for asphalt roofing manufacturing processes. The Fiberbed Mist Collector will reduce the buildup of condensables that form on the cold side of the RTO recovery bed, allowing the RTO to eliminate VOCs unburdened by the condensable portion of the emissions.
When selecting APC equipment for asphalt roofing manufacturing processes, manufacturers should consider the maintenance and downtime requirements of the APC equipment. To this end, there is a tradeoff between the size of the system and its upkeep. Compared to smaller equipment, large systems can operate for extended periods, lowering the frequency of maintenance and reducing the total amount of time the equipment must be offline.
Coalescing Fiberbed Mist Collectors from Air Clear minimize maintenance and downtime expenses. They are tested prior to shipment to ensure optimum performance in the field, and they operate continuously with little maintenance. When they do require attention, Fiberbed Mist Collector System filters are designed for quick and easy access. Cranes and overhead lifting equipment are not required to switch them out.
Maintenance
and Downtime
Air Clear’s RTOs also minimize the cost of equipment maintenance. They feature high-density ceramic insulation modules constructed to prevent spalling or erosion of the fibers, which would normally occur during heating when the fibers expand in different directions. The insulation system is efficient and durable, and requires little maintenance. Air Clear’s poppet valve design allows for ease of maintenance in the harsh conditions of the asphalt manufacturing process. The RTOs also feature long lasting, durable epoxy coatings.
Operating
Expenses
Air Clear’s RTOs also minimize energy costs. Their ceramic heat recovery beds capture and reuse up to 95 percent of the system’s energy. Further energy savings with a secondary heat recovery (SHR) system are possible, as the SHR recovers waste heat from hot combustion exhaust that is normally vented to the stack. A safe fuel injection (SFI) option lowers fuel use even further by eliminating supplemental combustion air needed for the burner.
A key factor that manufacturers must consider when selecting pollution control products for asphalt roofing manufacturing is the cost. Cost is more than just the upfront price to purchase the equipment. The total cost of a product has multiple components, including the expense of energy consumed to operate the equipment and expenditures for maintenance and downtime. Although investing in larger equipment generally involves higher upfront capital costs, savings can be realized over time. The increased scale of bigger equipment leads to higher energy efficiency, lower operating costs and less maintenance and downtime compared with smaller equipment.
Air Clear’s Fiberbed Mist Collector Systems exemplify this paradigm. With a large number of filters per system, their capital costs are higher. But their large filtration surface areas lead to lower total lifetime cost compared to smaller systems. This is because fiberbed mist eliminators with larger filtration surface areas have slower bed velocities and improved liquid drainage, resulting in lower pressure drops. Smaller pressure drops reduce annual electricity costs because less horsepower is needed to drive the fans moving fluid through the systems. More surface area also means lower filter replacement costs over the life of the systems as the time between filter element replacements is increased.
Air Clear designs and manufactures all of our pollution control products at our facility in Elkton, Maryland, which allows strict quality control and scheduling. Air Clear offers turnkey projects and service contracts.
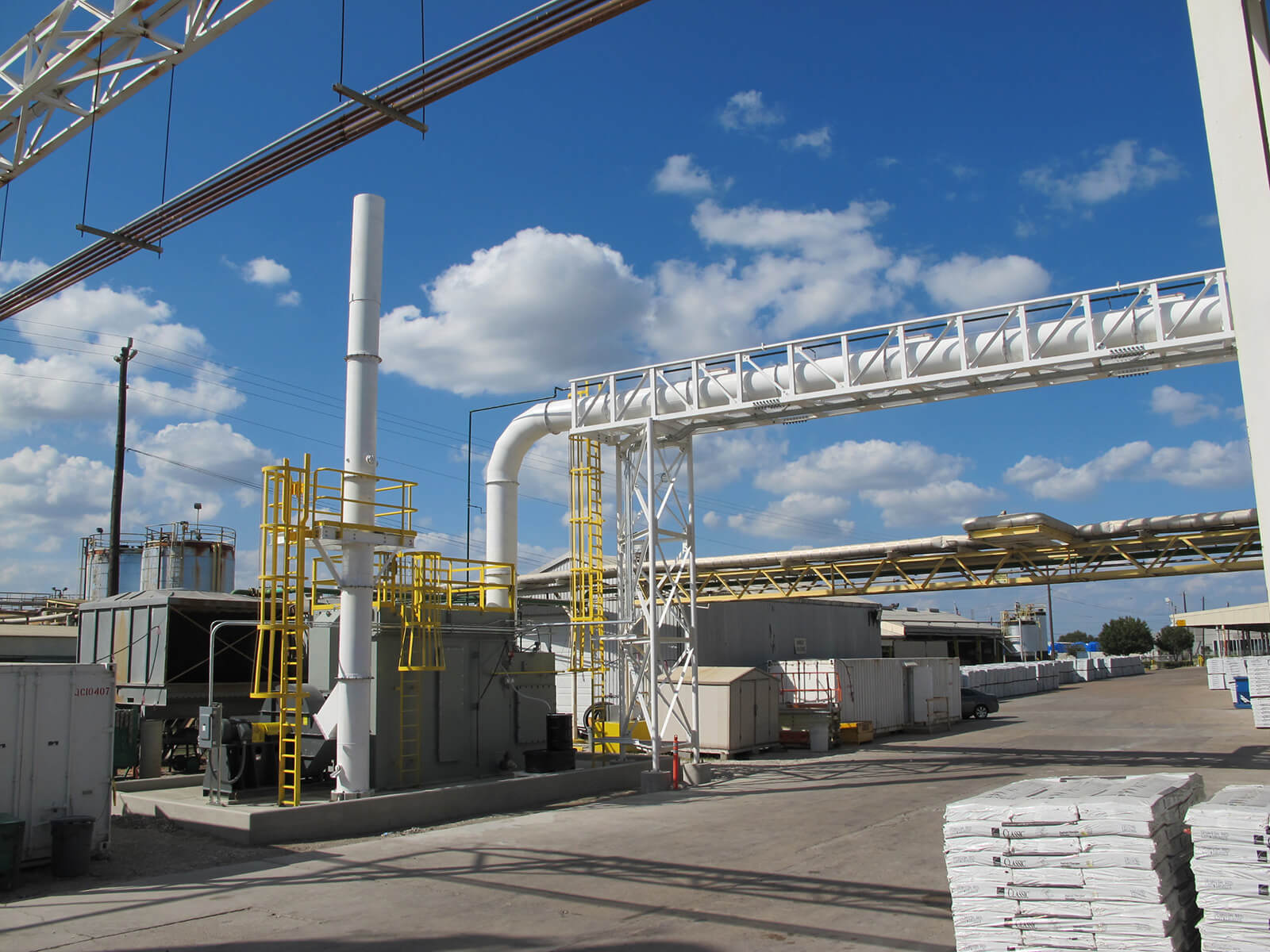
Figure 2: 13,000 CFM Fiberbed filter installed to control emissions on an asphalt coater/saturator. Zero opacity and three-year filter life are the system’s key attributes.
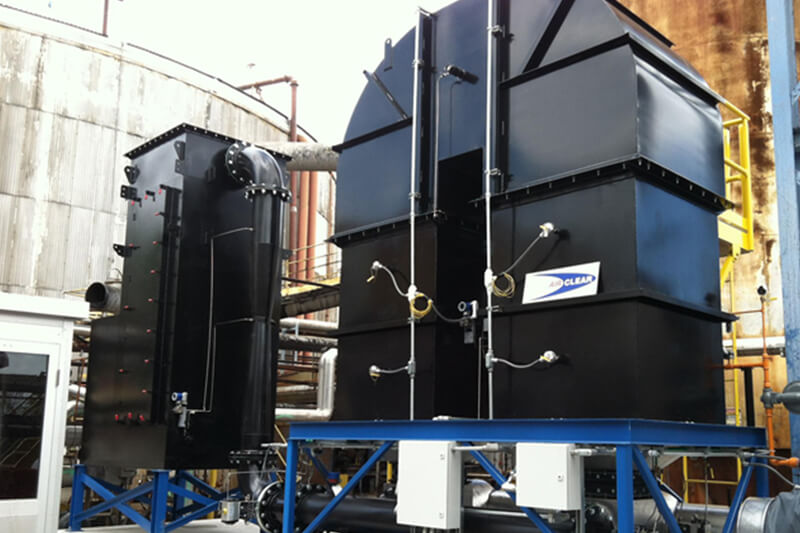
Summary
Hazardous air pollutants created as byproducts of the asphalt roofing manufacturing process must be mitigated. Fortunately, Air Clear offers a line of APC equipment that allows roofing manufacturers to control emissions cost effectively. By installing Air Clear Coalescing Fiberbed Mist Collectors and RTOs, manufacturers can remain in compliance with environmental regulations. Furthermore, these HAP filter systems are designed to operate with high energy efficiency and low maintenance and downtime requirements, minimizing total operating expenses.