Minimizing Emissions & Maximizing Output
The industry of dyeing & finishing textiles is crucial to the production of many materials including yarn, bedding, carpeting & clothing used in our daily lives. Textile manufacturing industry pollution from dyeing and finishing inherently creates visible fume emissions due to the vaporization of oils and chemicals into the hot Tenter / Stenter Frame oven process exhaust. These oil and chemicals condense, causing the “smoke” or “blue haze” emissions typical of these processes. The condensed vapors typically form submicron particles which are very difficult to control using common filtration systems. Traditional filters designed for dry particulate will not drain recovered mist well, creating the need for expensive frequent filter replacement. Electrostatic devices foul very quickly, again creating an expensive maintenance problem and production downtime, along with frequent Fire Hazards.
Air Clear Fiber-bed Mist Collector Systems offer the most advanced technology available for textile industry pollution air cleaning and heat recovery, all targeted towards improving your bottom line profitability. Whether you have a single Stenter Frame or an entire facility of Stenter Frames, Air Clear has the optimum solution to help you achieve EPA compliance and save money for your production.
Air Clear Fiber-bed Filter Mist Collector System have become the method of choice for controlling textile manufacturing, dyeing, and finishing industry emissions due to their high efficiency and low maintenance. Air Clear brings 30 years of experience with fiber-bed filter technology to a new level, ensuring your system will meet increasingly stringent air quality requirement for many years to come.
The textile industry stenter machine exhaust air is highly polluted with particulate matter, wax, fumes, oil aerosol, and odors. Green Initiatives for health and environmental concerns require technology to clean the air opacity and recover the heat energy for reuse. Air Clear Fiber Bed Filter Technology accomplishes both requirements and meet all Local and National Environmental Protection Standards. Air Clear is the only expert in the Textile Fiber Bed Filter Technology with over 30 years experience.
Electrostatic precipitators are use large amounts of electricity and require regular shut-down and time consuming maintenance. Install or Upgrade to proven technology for reducing your operating cost and meeting EPA compliance issues worldwide.
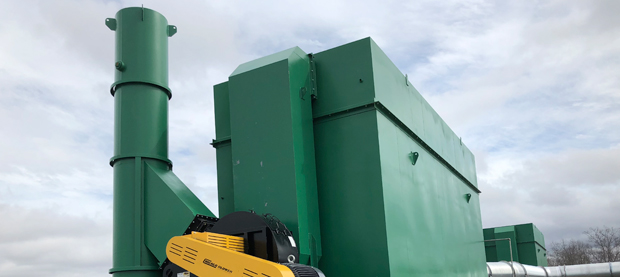
The Air Clear Fiber Bed Filtered
Mist Collector System
Serving the robust industry of textiles, Air Clear harnesses advanced technology to optimize efficiency & performance while mitigating textile emissions. The Air Clear FiberBed Mist Collector System can be integrated into any textile facility or single Tenter Frame to control harmful emissions, ensure equipment durability, and boost overall system efficiency.
The Air Clear FiberBed Filtered Mist Collector System has emerged as the industry choice for providing efficient, sustainable performance & cutting emissions. At the forefront of cost-effective textile emission mitigation, Air Clear guarantees that our clients are compliant with stringent local and federal air quality standards while maintaining long-term competitive advantage.
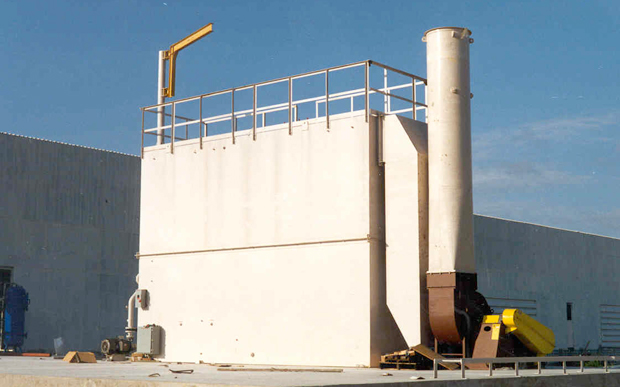
Features of the Air Clear
FiberBed Mist Collector System
- Brownian Diffusion FiberBed Filters to optimize efficiency & ensure under 5% opacity.
- Stack outlet particulate emissions reduced to under .01 grains/DSCF
- Effective Odor Removal technology
- Custom Design for Textile Dyeing & Finishing
- Continuous & uninterrupted operation
- A wide range of skid-mounting & control packages available to serve the unique needs of each system.
- Total Vendor Responsibility service & maintenance contracts to certify the Air Clear commitment to sustained success.
- Pre-tested equipment to guarantee optimum performance
- Cutting edge cooling systems incorporating water, air to air, & air to water heat & ambient air systems to address any diverse site requirements.
- Fast & seamless installation processes.
- Dynamic Pre-Filter Options including permanent, replaceable, & extended surface technology.
- Waste Minimization through innovative water-oil separation systems.
- Proactive Turn Key services provided from design, to permitting, to installation.
- Pilot Units available to verify high efficiency & sustainability on site.
Silicon & Teflon
Coating
Silicon & Teflon Coating has proliferated as an extremely effective industry in the production of materials like non-stick pans, safe packaging, & water-resistant clothing. However, the operation & application of Silicon & Teflon coating results in the harmful byproduct of volatile organic compounds (VOCs). Many operators in the industry have confronted obstacles with traditional technology that do not properly eliminate harmful emissions. In addition, standard filters corrode over time, losing efficiency and requiring expensive maintenance & replacement. As demonstrated by a recent case study, Air Clear can effectively meet the economic & environmental objectives of any Silicon & Teflon Coating Operation to eradicate VOCs & optimize savings & performance.
Client
Air Clear’s Regenerative Thermal Oxidizer (RTO) eliminates VOCs & boosts savings for Arlon Silicon Technologies
Case Study
Arlon Silicon Technologies, Rogers Corporation
Location
Bear, Delaware
Background
Arlon STD operates large Silicon & Teflon Coating operations with continuous fiberglass & additional woven material with calendars
Objectives
- Destroy 98% + of VOCs
- Utilize a cost-effective total system operation
- Return sufficient energy to limit oven burner energy expenditures
- Minimize production down time during installation of the new system
Solution
Air Clear engineers designed, fabricated, & installed a two-chamber Regenerative Thermal Oxidizer (RTO) with a hot bypass system, counter flow air-to-air heat exchangers, & an ambient air dilution valve.
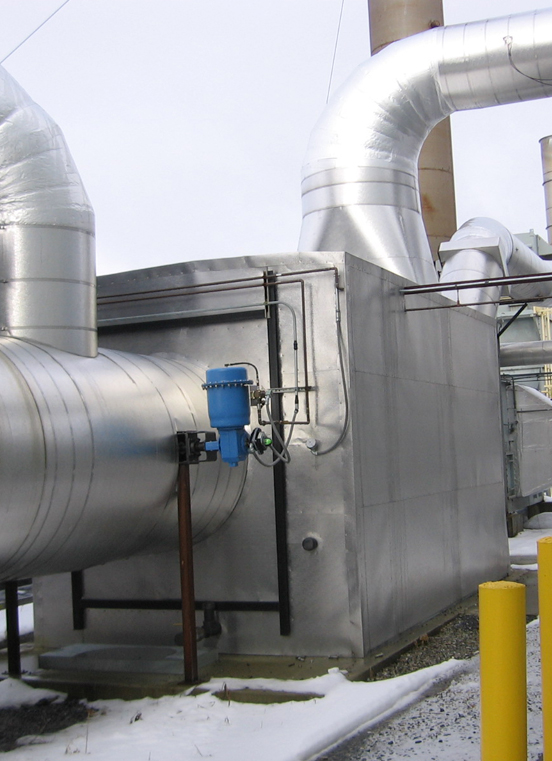
Air Clear successfully fulfilled emission requirements; exceeding 98% Destruction & Removal Efficiency (DRE) while producing approximately 7,900 SCFM of 375-400°F pre-heated ambient air for the drying/curing oven. The DRE is monitored by two FID monitors placed at the inlet & outlet of the RTO. The Lower Explosive Limit is also monitored on the outlet of the oven.
The heat exchanger operates with greater than 68% effectiveness. Once in operation, the RTO operated with zero fuel input while providing the required hot air to the drying/curing oven. The system is a two-chamber design, with poppet valves fabricated & tuned by Air Clear. This feature allows Air Clear to meet greater than 98% Destruction & Removal Efficiency.
The entire system was designed, fabricated & installed by Air Clear LLC located in Elkton Maryland. The system was installed in three weeks & was operational with the coating line operations within 36 hours of initial start-up. A PLC system was used to provide flexible, easy, remote operation of the RTO as well as the existing drying/curing oven as a complete system. In addition, Air Clear engineers can monitor & troubleshoot the system operation from anywhere in the World. Altogether, Air Clear delivered cutting edge technology that holistically met AST’s goals to eliminate VOCs, maximize energy efficiency, & ensure a durable cost-effective product from installation through operation.